Foamed Concrete Documentation & Technical Specifications
Foamed concrete documentation and specification sheets/ technical information can be found in the downloads below. And on this page. Please contact us with any specific queries.
Foamed concretes have several constituent materials that can be manipulated in their quantity to suit varying requirements. Typically, there are two main “driving” factors to a material technical specification:
- Strength
- Density
Often, one requirement will define the mix design. Consequently, this will effect a change to the secondary attributes. For example, thermal conductivity, fluidity, and, pour depth.
Foamed Concrete Capabilities
Foamed Concrete Technical Datasheet
High Density Foamed Concretes
Medium Density Light Weight Foamed Concretes
Low Density Light Weight Foamed Concretes
Ultra Low Density Light Weight Foamed Concretes
Primary Specification Drivers
Foamed Concrete Strength
The strength of foamed concrete is generally accepted as being between 1 & 10 Newton/mm2. However, strengths up to 25 Newton/mm2 at 1400kg/m3 have been produced in laboratory tests. But, these materials are not commonplace in practice on site.
Over the course of 30 years, Propump have designed many Foamed concrete mixes. In turn, each of these mix designs have different water / cement ratios. In addition, volumes of aggregates, foam and admixtures change.
Generally, common strengths that specifiers choose for foamed concretes’ range from 1N/mm2 to 5N/mm2. However, higher strength foamed concretes up to 10N/mm2 can be manufactured when requested. Subsequently, these tend to be for critical, or specific applications.
For example, a 1N/mm2 is a common specification for a foamed concrete. Applications include; temporary works, sewer and pipe fills, vault abandonments and mass void filling. Comparatively, a 1 newton/mm2 mix is achievable at densities of 500kg/m3, 750kg/m3, or 1000kg/m3. Furthermore, each of the densities achieving 1 Newton/mm2 will have a different mix design.
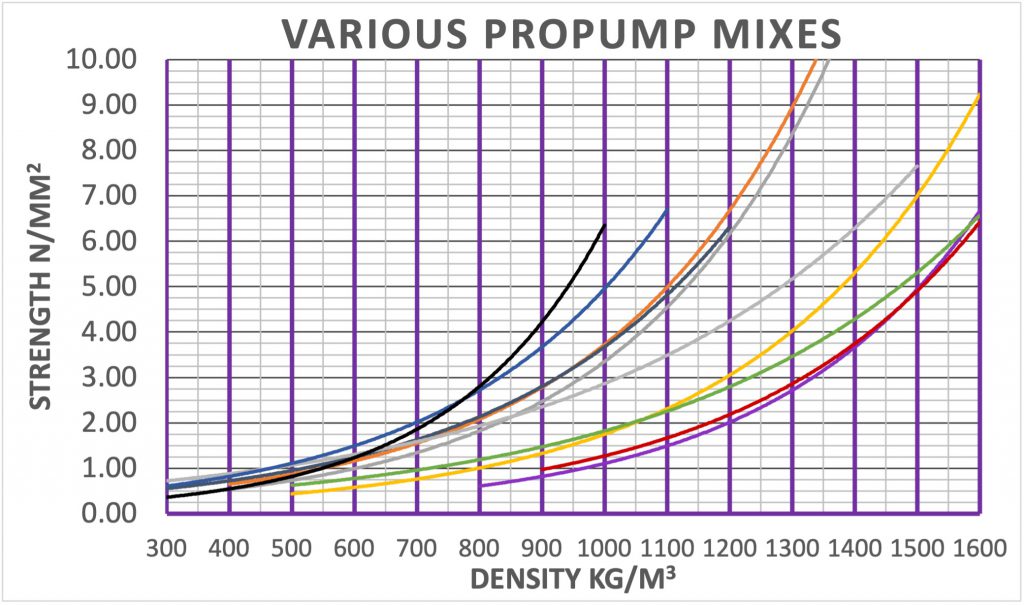
The effects of foamed concrete density, cement type and content, water/cement ratio, foam type and curing regime will influence the compressive strength.
Foamed Concrete Density
Historically, the definition of a foamed concrete is a material that has an air content of over 20% by volume. It typically involves a mechanically formed foam which is blended into a grout or “slurry” mix. As a result, this broad definition can include a range of densities with anything lower than 1800kg/m3 being considered a foamed concrete.
Heavier foamed concretes, such as 1600kg/m3, tend to be manufactured and pre-blended. Because they have a low volume of foam entrained into the base mix, these mixes have higher strengths. However, they have lower pump-ability because they are thicker and drier. Consequently, foamed concretes in this density range are used almost exclusively for road re-instatement works and narrow trenches.
The densities of foamed concrete produced by Propump engineering on a typical construction site, range from 400kg/m3 to 1500kg/m3. On one hand, densities below 400kg/m3 need to be attempted and undertaken with care, using specialized curing systems. Whilst Foamed concretes heavier than 1400kg/m 3 can require extra care when pumping, due to their high solids content with little relative foam.
Propump Engineering have designed and manufactured bespoke “inline” foam production systems. These produce foam simultaneously as the base mix is pumped. In turn, this in-line mixing means that a complete delivery of material from the ready mix supplier of 6m 3 is processed with the foam added during the pumping phase. For example, manufacturing a 500kg/m 3 foamed concrete on site using Propumps’ inline system means that every 6m 3 of base material delivered to site makes 25m 3 of foamed concrete at the point of delivery.
Foamed Concrete Technical Attributes
The materials used to produce a foamed concrete fall into three main categories. These will effect a change in the wet and/or cured concrete.
We will assume the water has very little influence on the foamed concrete. Provided that the source is potable and therefore a constant, the three categories are:-
- Cement type
- Filler or aggregate
- Foaming agent
Cement Type
The cement or binder is used to affect a set in the liquid foamed concrete creating a solid mass.
The set time is created by careful selection of the correct materials to suit the application and location. For instance, set times of Propump mix designs are normally between 2 and 8 hours
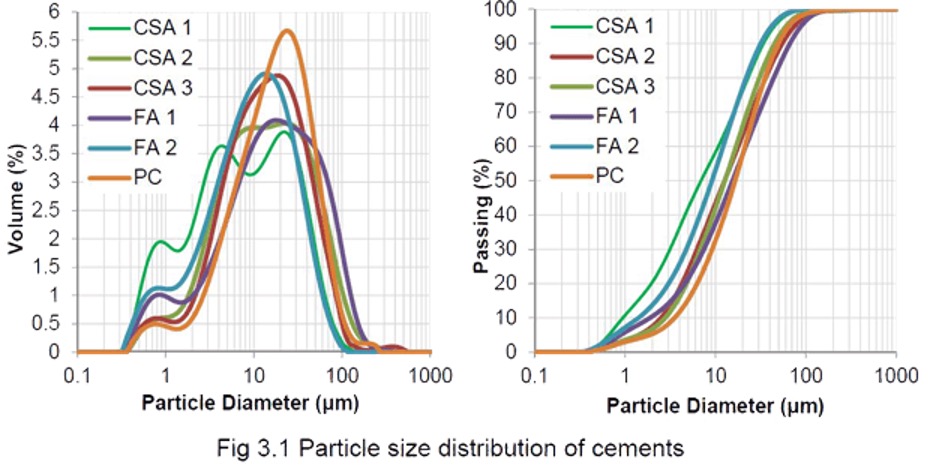
The cement types fall into sub categories which are listed below;
1a. Ordinary Portland Cement 52.5N, 42.5N, 32.5N.
Propump mix designs incorporate 200-400kg/m3.
1b. Rapid hardening Portland Cements (RHPC).
Propump mix designs using RHPC incorporate 200-400kg/m3.
1c. Blended Cements using Fine Pulverized Fuel Ash (PFA f ) from coal fired power stations.
Propump mix designs may incorporate up to 70% replacement PFA f.
1d. Blended Cements using Ground Granulated Blastfurnace Slag (GGBS).
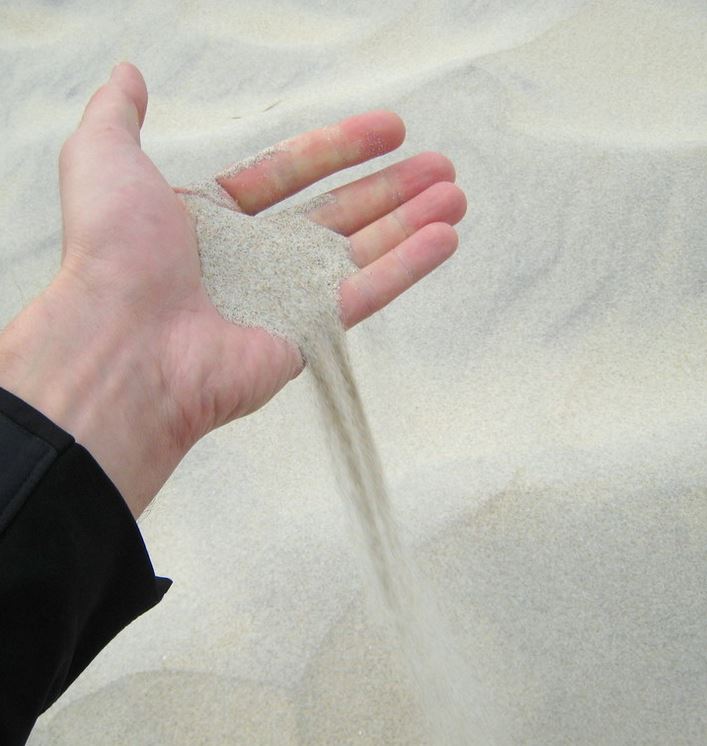
Filler or aggregate
Propump mix designs incorporate fine aggregates with a maximum particle size of 5mm (except for light weight aggregates). The aggregate grading should be even, with greater than 50% passing a 600µm sieve. Due to their weight, and size, Larger aggregates will precipitate causing a poor quality of set material.
Fillers in Propump mix designs include;
- Marine sand
- Land dug sand
- Chalk
- Crushed concrete
- Crumbed Rubber
- Granite dust
- Limestone fines
- Lytag fines
- Expanded polystyrene
- Coarse Pulverised Fuel Ash (PFA)
Foamed Concrete Foaming Agent
Propump foaming agents are used to create a pre-formed foam similar in appearance to a shaving foam. Due to the high expansion required, foam is produced through a specially designed generator by combining hardware, air and chemicals. To that end, the result is a foam designed to provide excellent wet concrete stability and outstanding cured properties.
Propump26
Protein based foaming agent designed by Propump. It is used to provide a highly versatile foam and is suitable for use in materials from 200kg/m3 to 1700kg/m3. We are very proud of its performance levels. For this reason, it’s used directly by Propump to service its extensive UK and Overseas client base.
Propump40
A concentrated version of Propump26. Therefore it is used where greater viscosity is required. As a result, Propump40 has been used to produce significantly lighter foamed concretes. Whilst also achieving a lower water content. Additionally used to minimize material loss on voided infill such as mines.
Note: Protein based foams are only suitable for “dry” foam generators
Propump synthetic
Manufactured to closely duplicate the protein foams. Synthetic foaming agents are extremely active. Therefore requiring much less energy to create foam. Consequently, synthetic foams are normally used through a wet foam system to produce heavier mixes (1200-1700kg/m3). However, it can still be used for both the dry foam system and the wet foam system.
Fire resistance
Propump Foamed concrete is extremely fire resistant. Therefore, suited to applications where fire is a risk.
Tests have shown that in addition to prolonged fire protection. The application of intense heat, such as a high energy flame held close to the surface, does not cause foam concrete to spall or explode as is the case with normal density concrete.
Thermal insulation
The Thermal insulation value is the ability of a material to resist the flow of heat across it. The rate of heat flow is known as the K value. Hence, the lower this value, the higher the thermal efficiency.
The table below shows the K value for foamed concrete lies between 0.08w/mk at the lower densities and 0.62w/mk at the higher densities.
Density | W/MK |
---|---|
400 | 0.08 |
600 | 0.1 |
800 | 0.14 |
1000 | 0.22 |
1200 | 0.35 |
1400 | 0.5 |
1600 | 0.62 |
Foamed concrete characteristics
Foamed concrete is usually a pumpable, free flowing material. Therefore, it requires no compacting and can be poured in consecutive layers up to 1 metre in depth. Propump place foamed concretes that will search and encapsulate with ease. In addition, foamed concretes are, to an extent, self-levelling. They will freely flow upwards of 30 metres.
Benefits
- Pumpable
- Reduced labour / manpower to place
- light weight
- self-consolidating
- no vibration required
- insulating
- easily machinable / re-excavatable
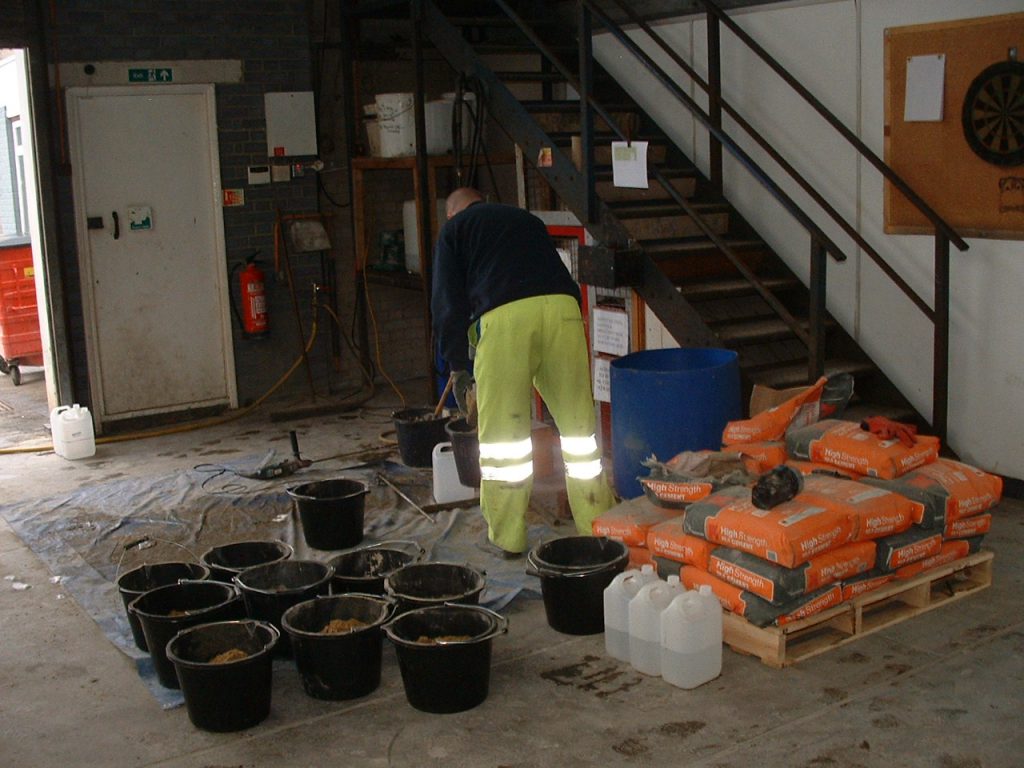
More information
Propump Consultancy Services
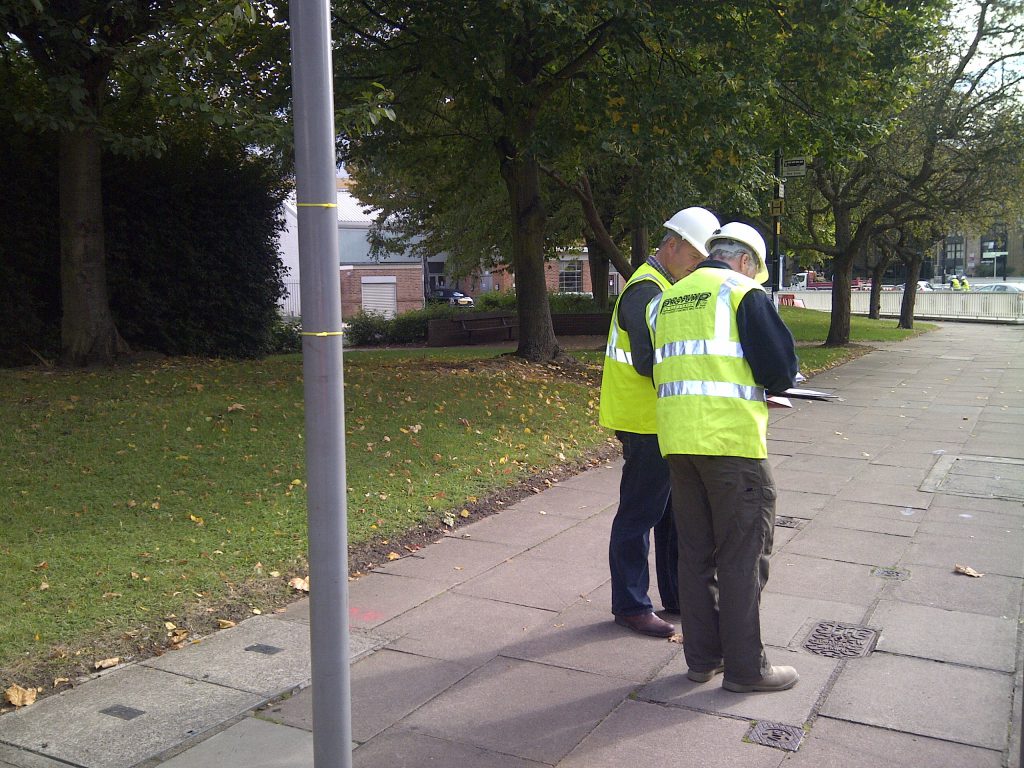
Propump news & articles
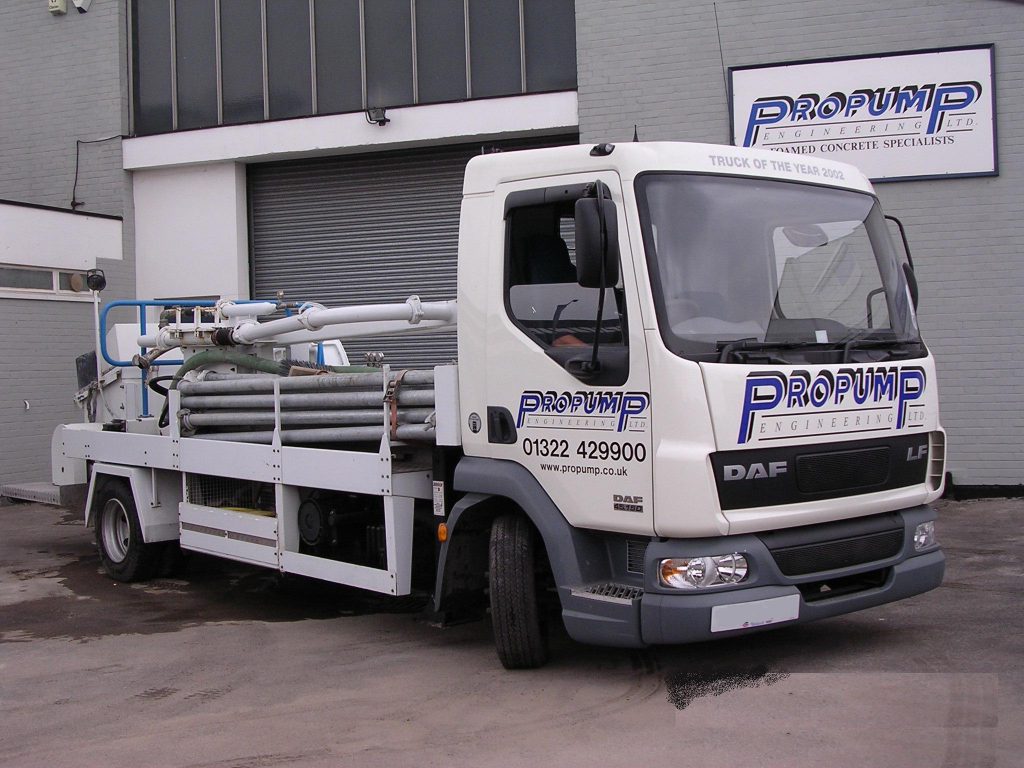
Why choose foamed concrete?
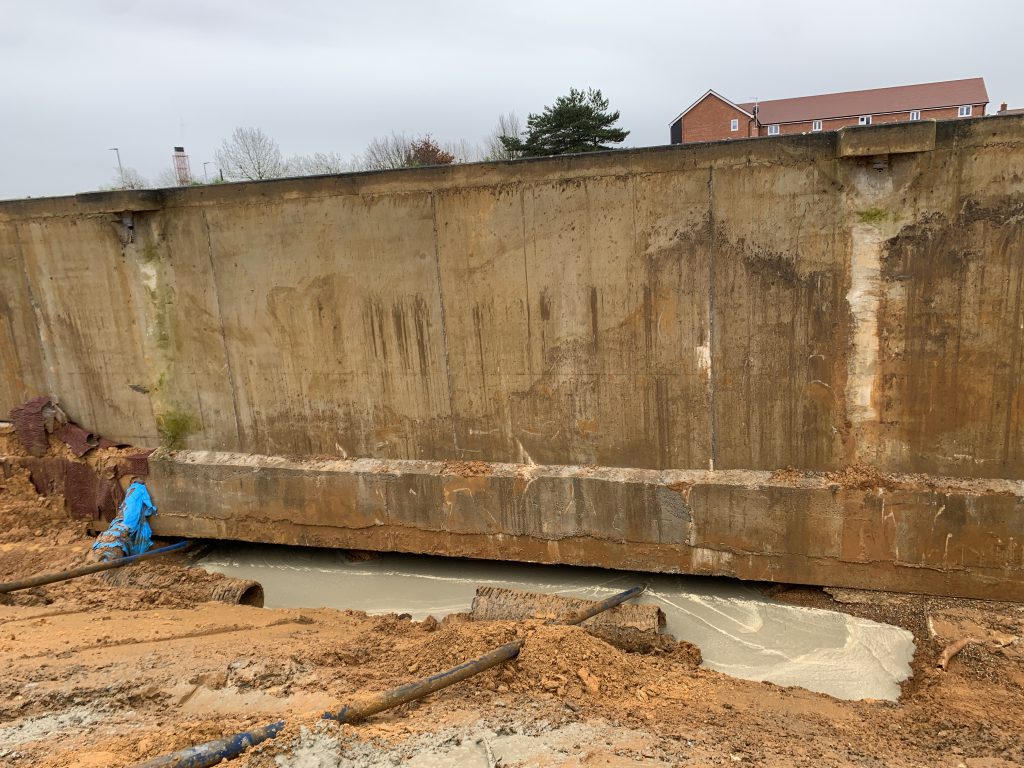
Projects by Propump
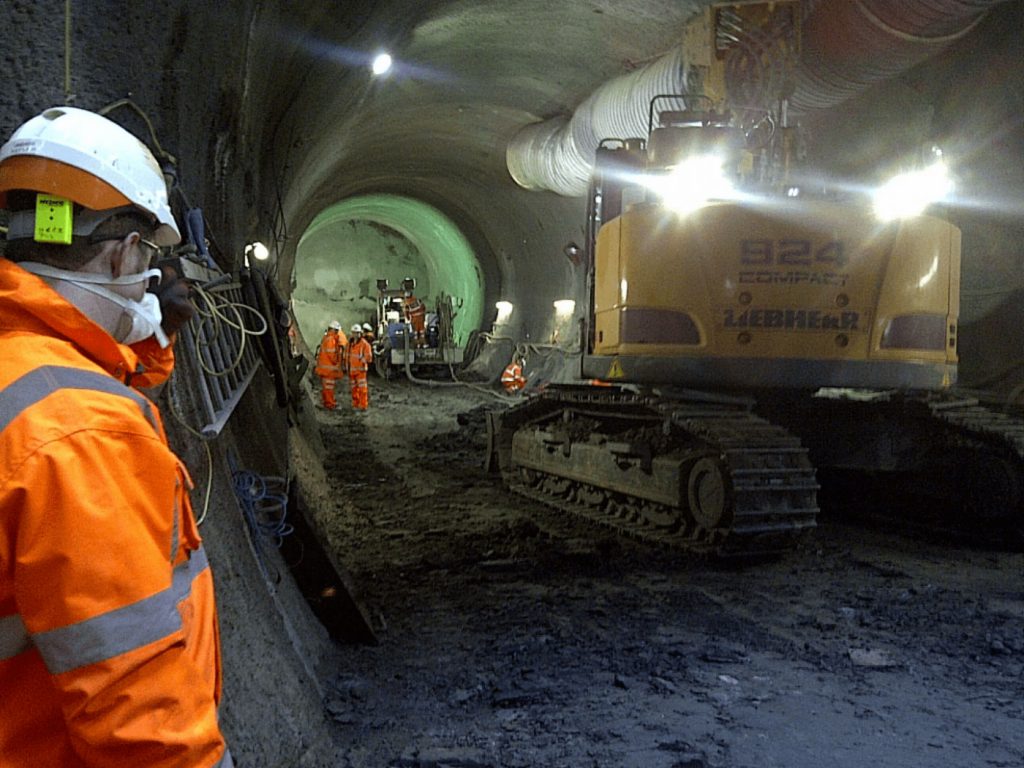