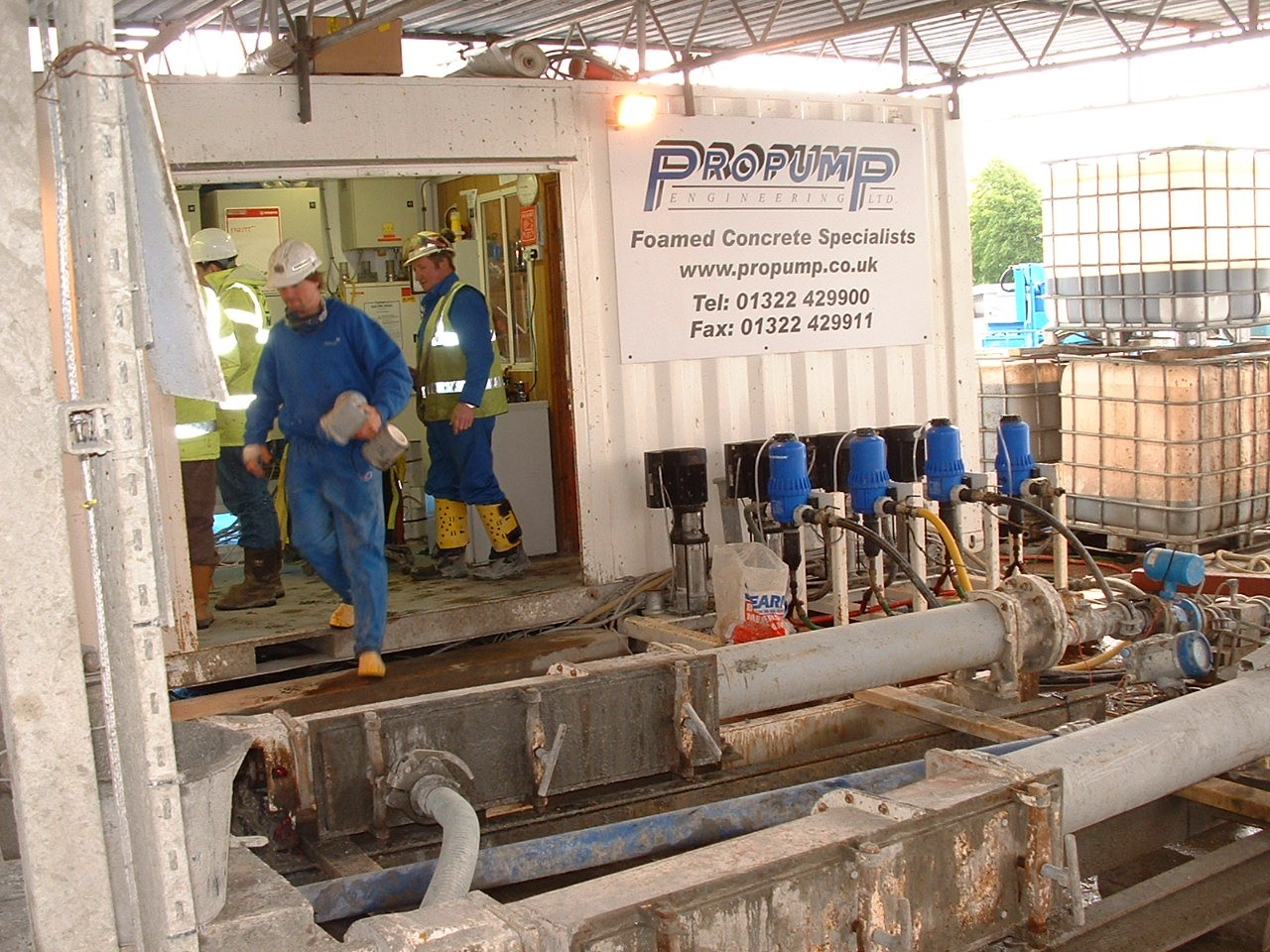
The History of Propump
The History of Propump Engineering – the foamed concrete specialists
Before Propump. Before Foamed Concrete. Trevor Ansell was a young 24 year old engineer, working as a salesman for a pump manufacturing company. Whilst networking at a highways and Utilities exhibition, he introduced himself to two gentlemen, Mr Jones and Mr Taylor.
Mr Jones and Mr Taylor turned out to be from the British Cement Association (BCA) and they were there promoting a new material called Foamed Concrete for the use in trench reinstatement.
In order to produce Foamed Concrete, not only were pumps required, so were chemicals, sand, cement, water, mixers and something need to make the “foam”. To a young, ambitious, engineer this was close to heaven, solving problems, improving designs and performing experiments. This resulted in the first portable air operated foam generator.
The foam
It was about this time that Trevor contacted Cormix chemicals who supplied samples of a synthetic foaming agent along with some details of what dilution rate and expansion could be expected. This led to many hours of producing foam to prove the chemicals were stable and consistent.
The concrete
The puzzle still required some concrete to put the foam into and create the magical foamed concrete. Ernie Moss, another Cormix employee, worked out of the Greenwich laboratory proving mix designs and chemical dose rates for the range of Cormix products. Here Ernie and Trevor set about testing mixes and designs that could be used.
A typical 1980s concrete test lab consisted of; test cube water tanks, creteangle mixers, shelves of chemicals and bins with aggregates and cements. All housed under a flat roof with a small office attached. Here they made several mixes of foamed concrete using Cormix chemicals and documented the results. This was as far as the time would permit us to go without deciding to setup a company.
In 1991, two lifelong friends, David Aldridge and Trevor Ansell decided to form Propump Engineering. Originally, the company was born with the sole intention of manufacturing equipment.
David, also an engineer, was working for a civil engineering land survey company at the time, so he had a number of contacts within the construction industry, who it was felt would be very interested in what the two men were offering.
This equipment would primarily be used by contractors to produce volumes of foam and mixed into Pre formulated “grouts” to produce a foamed concrete that met the specification requirements for the “New Street works and highways act”. The new Street works Act was a way of ensuring Reinstatement works were installed properly by demanding a 24-month guarantee on each job. This had the effect of pushing contractors into striving for a first-time permanent reinstatement.
Propump would make its fortune selling equipment to every contractor in the UK who was undertaking trench reinstatement work.
Or so they thought.
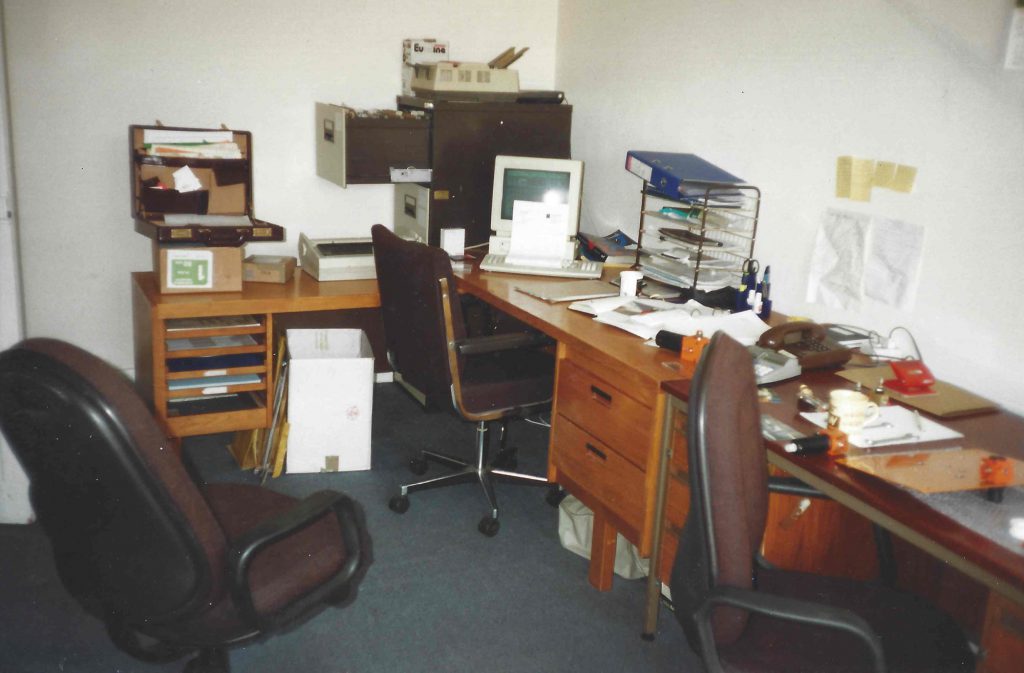
“Within 2 weeks of starting Propump we were approached by ALHCO who were working on the Jubilee line extension. Enabling works at Westminster comprised the requirement to place foamed concrete. We had every intention of just supplying a foam generator and instructions so ALHCO could undertake the works themselves. However, ALHCO had other ideas and we ended up supplying the foamed concrete (110m3) using the foam generator that they agreed to buy. We found out some years later the foam generator was never used again!”
Deliberations following the ALHCO job quickly led the Directors to the decision that the right avenue was in contracting and not equipment supply.
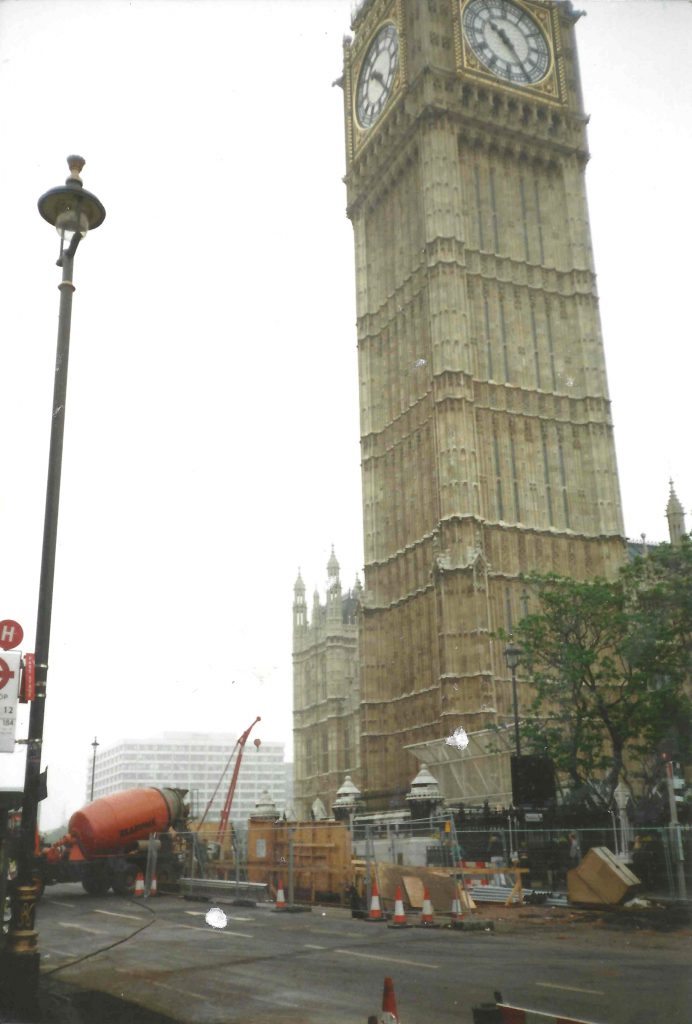
The first years in business saw the company move into its first premises; a shared location in Bromley near London with a small office and workshop area with some outside space for chemicals and equipment.
Early awards
The bank entered Propump into a competition for the best new business in the County. Some photos were taken and a brief question and answer interview scripted. It was a delight to find out we had won and would be entered into a Southern competition pitting us against many other companies across the south of England. We won this too and were invited to a large corporate function for the awards to be presented.
Approximately 2 weeks prior to collecting the best new business award, Balfour Beatty (a large and prominent construction and utilities company) at Heathrow airport called with an urgent Job. They told us to “drop everything we were doing and get to Heathrow with all the equipment and chemicals we could muster.”
There had been a tunnel collapse and our services were required 24/7. At this point, in the company’s history there was only David and Trevor, finding extra hands to work for us was a new experience.
For the first 10 days or so both men lived on site out the back of a hired Transit van and worked in shifts grabbing a few hours sleep when they could. The chance of promoting the company at an awards ceremony was only a few days away. A few people (friends or family) were persuaded to undertake the work at Heathrow in order to get home and clean up before the night out.
“We managed to convince my brother in-law and an old work college to takeover for 12 hours while we sped home and readied ourselves for an evening out.” – “The awards were at the Hilton Croydon, with the evening hosted by David Frost who presented our award to the song “Simply the best” by Tina turner, which still makes me smile today.” A few beers and after a few hours later we are back home for some sleep before it was back to the real job.
In the end, over 14,500m3 of foamed concrete had been placed by Propump Engineering at terminal 4 to prevent the tunnels from collapsing.
“I can remember walking along a line of concrete wagons all carrying materials for us and waiting to be pumped into the tunnels. I counted 75 6m3 concrete trucks on site at the same time”. Every plant in the vicinity had been hijacked by Balfour Beatty to prevent what could have been an even bigger catastrophe than it already was.
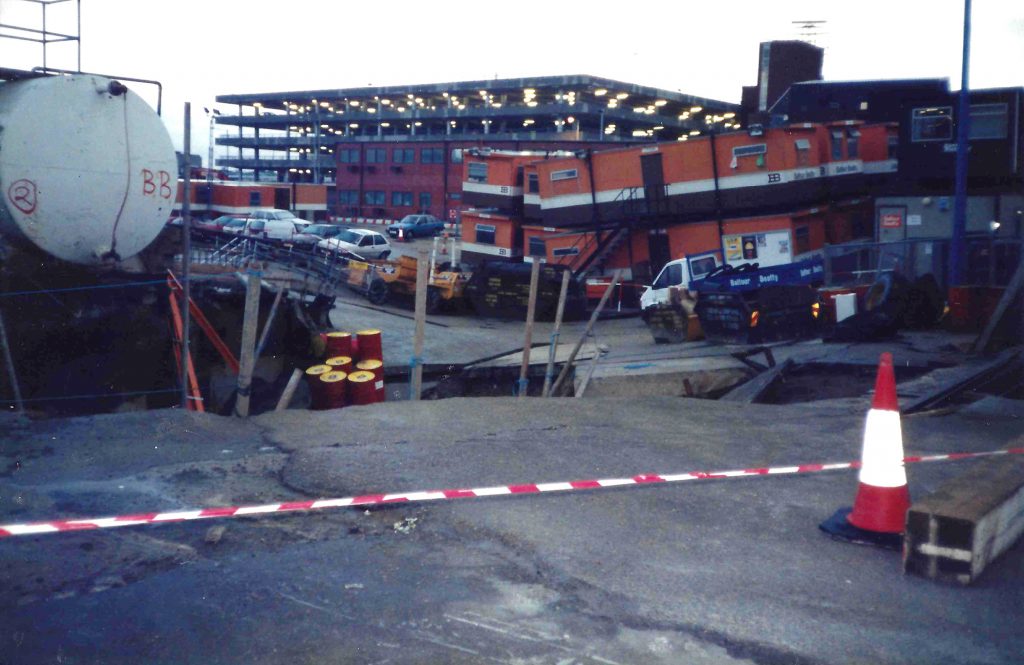
Propump now employed 2 full time operatives and a sales manager. The company moved on from Bromley into a larger premise in Dartford, the offices and workshops required renovating and altering to suit the specific needs.
Developing materials and equipment
It had become apparent that we needed to develop our own chemicals and mix designs to establish Propump as a company with the knowledge required to. The next few years we formulated blends of Hydrolysed Protein using different molecular weights and additives to achieve a foam which was stable, balanced and produced higher strength materials than the synthetic materials we had used to date. The product we produced Propump26 and Propump40 are still at the heart of our operations today being used all over the world by various associated companies.
The next challenge was to develop the in-line pumping system. We had read about such systems in Holland but had never seen one. when the opportunity to purchase a grout pump on a truck chassis was offered we decided to purchase it and set about converting it to foam in line with our mix designs and chemicals. The first unit would process a 5m3 delivery of base materials into a 1100kg/m3 density foamed concrete in around 25 minutes producing 10m3 of foamed concrete. This pump system was used for many years and set the scene for the future of Propump.
The red “dodge” was the first inline foaming system owned by Propump, several iterations have followed it since the mid 1990’s.
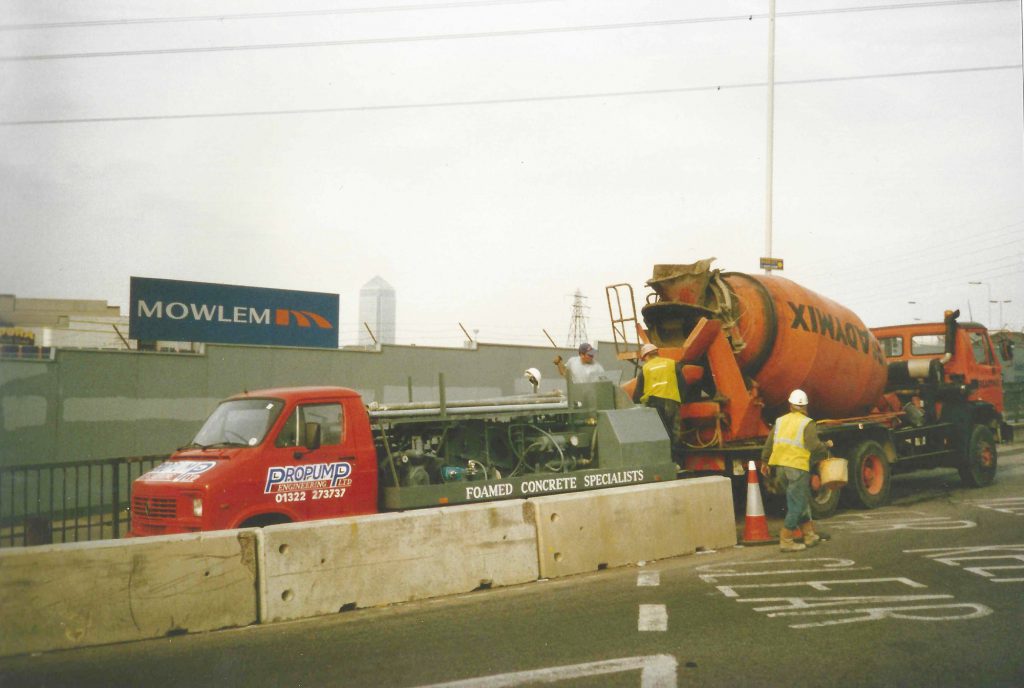
The new design pump was larger and more capable, processing a load in around 15 minutes and capable of producing a 400kg/m3 density material.
Two more machines were built on new chassis at even higher outputs; they could now process a 7m3 delivery in 10 minutes making it one of the fastest capacity machines in operation.
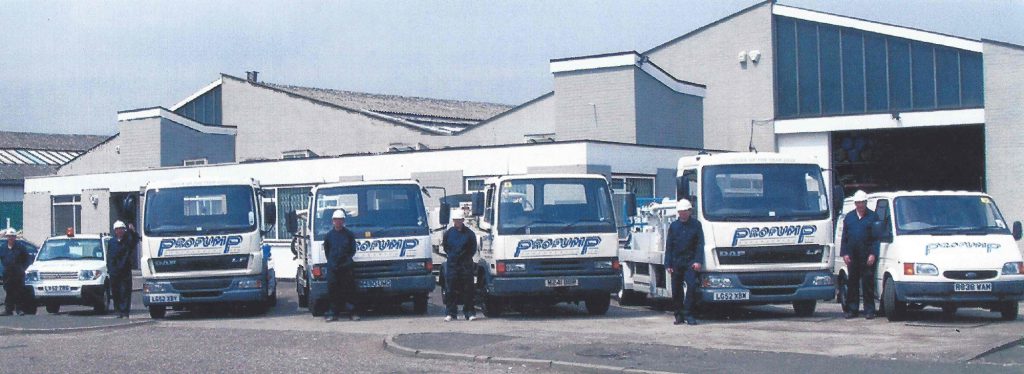
Ultra light densities
The Canary wharf development used foamed concrete in the construction of the roadways and Propump had already placed many thousands of metres of foamed concrete at a 500kg/m³ density. Many engineers were now interested in the production and use of light weight foamed concretes, the method of production brought a much needed boost in onsite efficiency and quality control of materials.
Combe Down mines
Combe Down, Bath, famous for its roman spa and for its lime-stone. The latter posed an urgent safety concern. The pillars holding up the mines beneath large areas were at risk of collapsing, a plan of void filling and The criteria being a low strength free flowing material required pumping large distances. Propump were contacted by the consultants and minor works contractor Hydrock Engineering and between the two companies we undertook some initial stabilisation works to prove the material was suitable. Over the coming years various stages of works were released and Propump/Hydrock successfully won the work thus completing the filling of Combe Down mine with some 600,000m3 of foamed concrete. We developed computer-controlled systems for Combe Down which pumped the material up to 1000 metres into the mine and then added the foam required to achieve the correct density. At times we had 7 units simultaneously pumping material from a centralised batching plant. The working day was between 8 am and 4pm with deliveries of cement only allowed between 9.30am and 3.00pm so on a good day we could use 450 tons of cement or 15 tanker deliveries. Output was up to 1,500m3 a day with averages not far behind that.
Propump has travelled the world with its products being used in many countries including Australia, New Zealand, Sri Lanka, France, Germany, Cyprus, Barbados, Iran, Morocco, Singapore, Malta, Indonesia, Ireland, Sweden, Denmark, Poland, etc.
Clients we have worked for include, the Nuclear Industry, Power networks, London Underground, Rail networks, and most of the major civil engineering companies. With a growth in the use of foamed concrete there has been an increase in the study and development of the material through University and commercial investigation. Projects to explore the use of foamed concrete for Roads and Highways has quickly been surpassed by Insulation properties, sound attenuation, fire resistance, encapsulation of waste materials, floating pontoons for fisheries, reclaimed land projects, the list is endless.
2020 onwards. What is the future for foamed concrete and what can we expect to happen in the coming decades? The extremes of the spectrum will be pushed with ever decreasing densities and increased strengths. We will see an increased use of waste products in combination with cement alternatives to lower the carbon footprint of concretes in general.
More information
Propump Consultancy Services
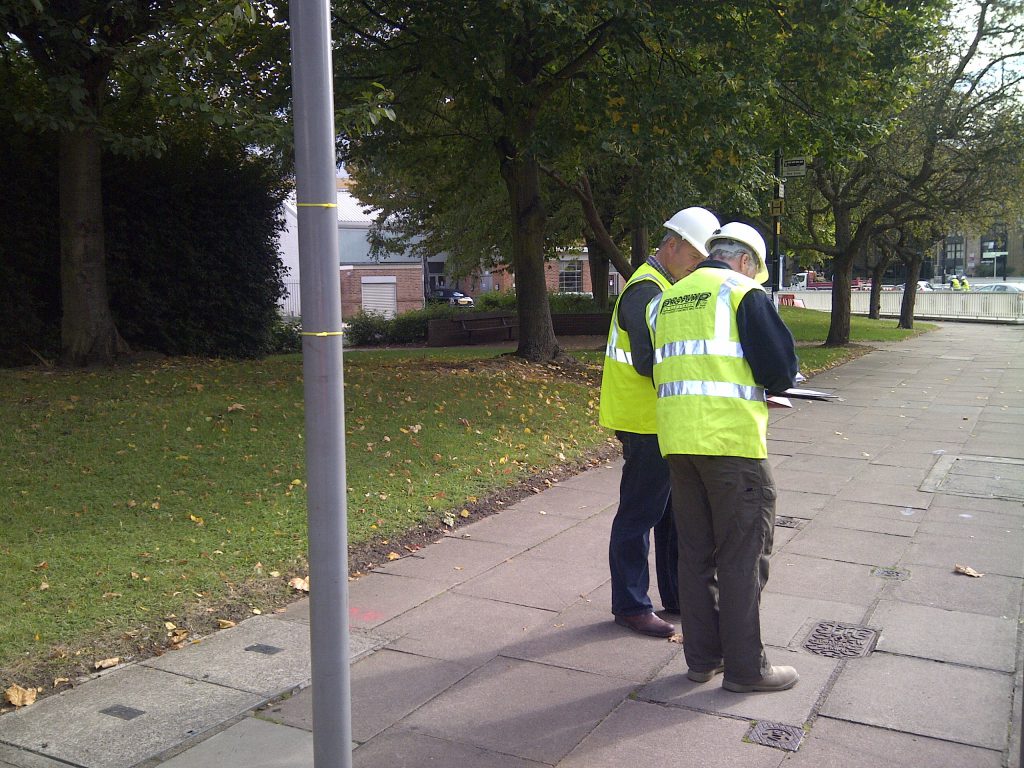
Propump news & articles
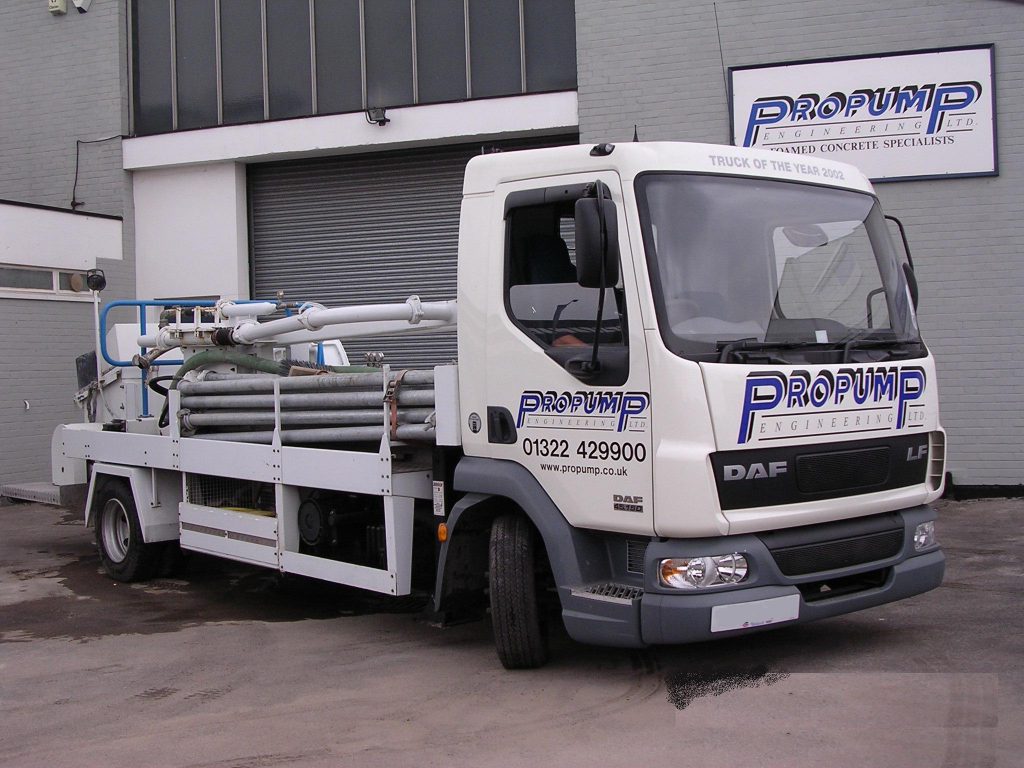
Why choose foamed concrete?
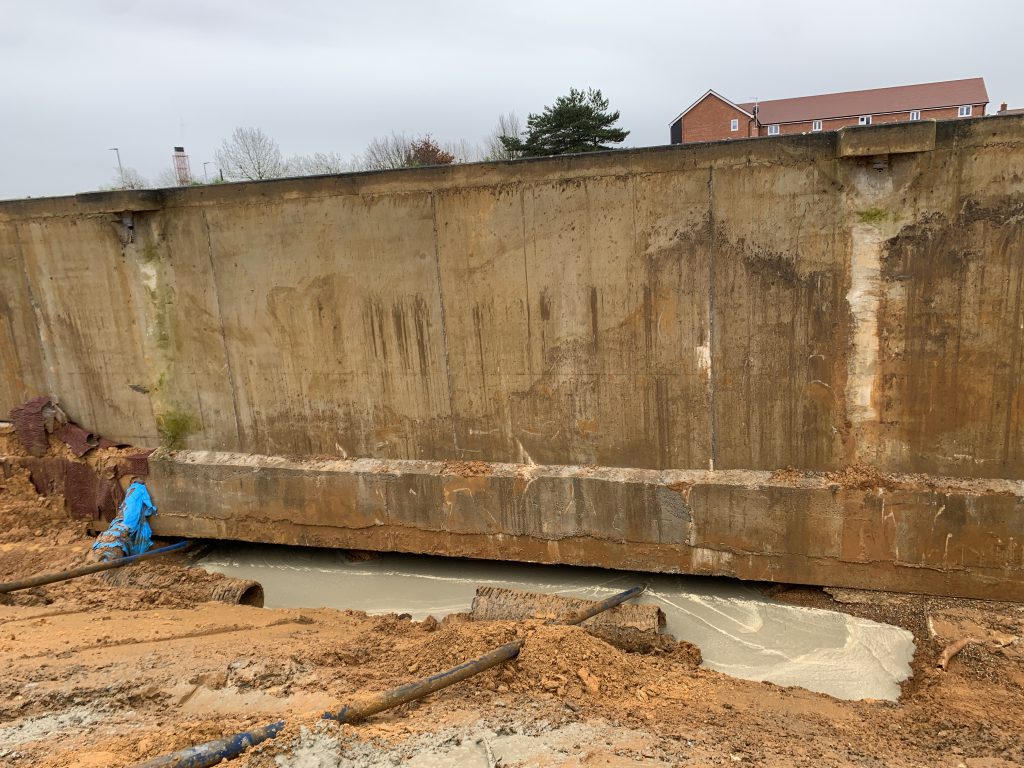
Projects by Propump
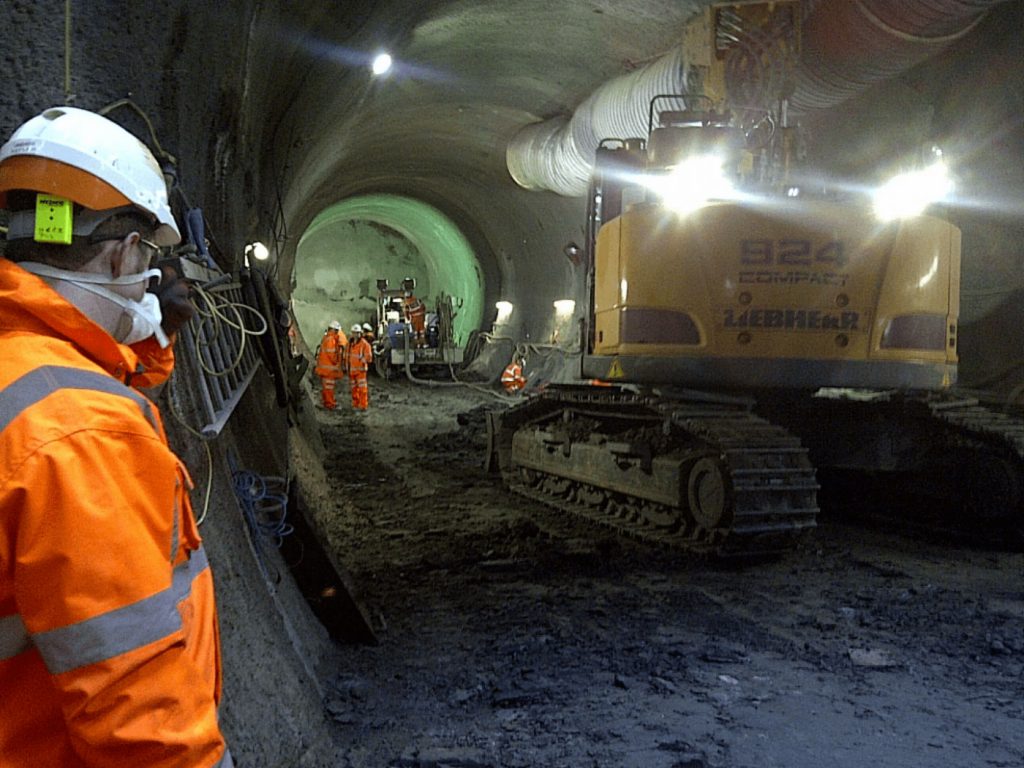
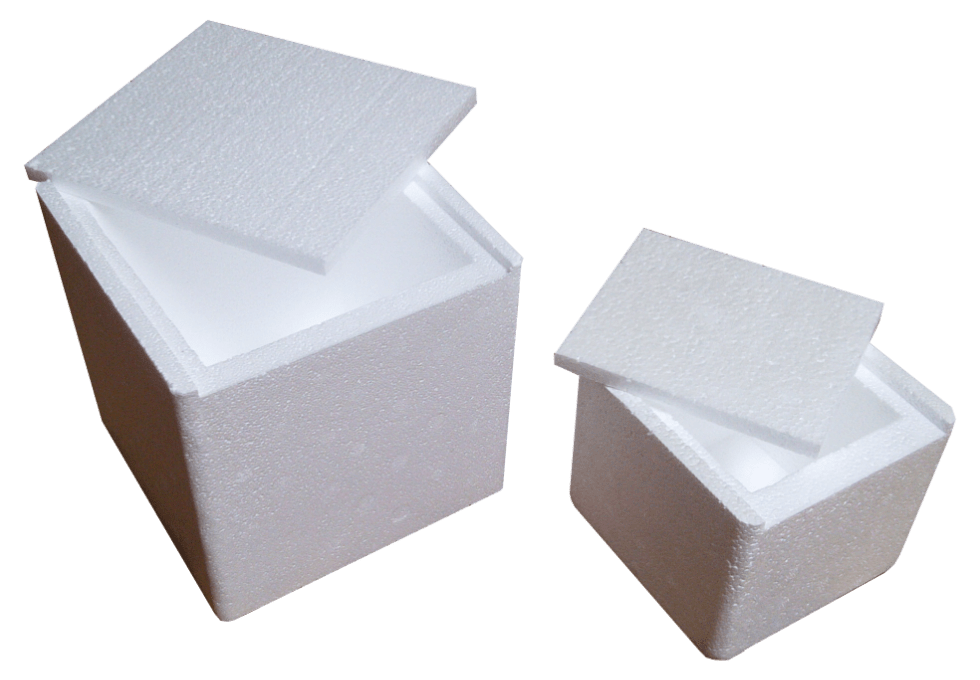
Foamed concrete cube moulds
Large quantities of both 100mm and 150mm foamed concrete cube moulds are kept in stock, available to purchase on a next day delivery.
Please call the office for up to date prices on 01322 429 900 alternatively email info@propump.co.uk